How to combat production delays with a supply chain solution
No one likes waiting, especially when it comes to getting your products to your customers on time. Unfortunately, production delays are sometimes inevitable. These delays create a ripple effect, disrupting schedules and customer shipments. Missed shipments can affect customers’ deadlines, impacting revenue and their relationships with trading partners. Production delays can stem from too much downtime after an equipment breakdown or a lack of necessary materials, leading to major inefficiencies.
While these delays may be inevitable, there are still steps manufacturers can take to reduce the frequency or effects of production delays. Reducing production delays boosts productivity, customer satisfaction and savings.
What causes delayed production?
When you’re working with many partners within a multi-faceted supply chain, there are always going to be elements that are outside of your control. It’s important to understand how and why unexpected obstacles can cause production delays.
Stockouts
Missing any necessary raw materials? Expect production to halt, which leads to bottlenecks and longer lead times. When you don’t have access to every single material you need, you can’t make your product and will need to reconsider your re-ordering process and lead time.
Supplier delays and supply chain disruptions
Up to 70% of supply chain issues occur pre-shipment. Raw material shortages, transportation issues and late supplier deliveries can all have a ripple effect across all aspects of the supply chain. When this happens, rescheduling production runs can really extend the amount of time to customer delivery.
One beverage supplier uses the example of a four-week window. If they don’t have everything they need to stage and run the line, they miss their production window and are delayed an extra four weeks until their next scheduled run.
Lack of transparency and timely communication
Many manufacturers lack visibility into their orders and inventory. Without real-time data and effective communication with partners, production planning becomes a challenge. Timely updates on inventory levels and order status are crucial for avoiding bottlenecks and delays and ensuring smooth operations.
Labor shortages
Since 2020, finding skilled workers to run manufacturing equipment has been a challenge. Production often gets delayed because there aren’t enough staff to operate lines and/or machinery. Without these skilled workers, there’s no one to ensure products are able to be made.
Recently, many companies have reported plenty of job openings they have been trying to fill, further supporting the claim that there is no job shortage but merely a labor shortage.
Equipment malfunctions
Equipment malfunctions are bound to happen, especially when working with aging machinery and maintenance. Even if you have the right parts and personnel, repairs may be easier, but any lapse in production still causes delays. Of course, the sooner these repairs can be made, the better.
Poor planning and forecasting
Demand planning and forecasting isn’t a science—it’s an art. When there’s misalignment between demand forecasting and production capacity, companies may need to juggle their schedules to ensure products go out on time. A lack of planning will always catch up to manufacturers.
What are the effects of delayed production?
Delayed production is more than just an annoying setback. It can be detrimental to a business, especially when they value customer experience and vendor partnerships. It can also have a major impact on your business’s bottom line.
There are many effects of delayed production that you may not realize, including:
- Increased costs: employee overtime, expedited shipping fees and penalties for missed deadlines.
- Customer dissatisfaction: loss of business and damaged relationships.
- Supply chain backlogs: cascading delays that affect the entire production and supply chain.
- Negative impact on competitiveness: risk of losing market share to more agile competitors.
- Damaged partner relationships: unhappy vendors may choose to halt business with your company.
How can I combat delayed production effects?
While you can’t predict the future, you can prepare for it. With strategies from your supply chain partner, you can take a few steps that lead you in a more positive direction when the next production delay occurs.
Optimize your supply chain management
Build stronger relationships with reliable suppliers to mitigate the risk of delays. Diversify your supply sources, so you have other options if the delay originates on their end.
Implement predictive maintenance
Integrate new technology for proactive maintenance to reduce equipment downtime. When you can see that equipment will need to be updated soon, you get ahead of any delays.
Stronger workforce training and flexibility
If your workers are cross-trained to adapt to production shifts, you can minimize delays. Promoting flexible employees can help when things start to go in an unexpected direction.
Automate purchasing and procurement processes
Avoid relying on paper, email and phone-based order updates, which are slow and open up room for error. When you have the right visibility into your supply chain, you can assess and pivot quickly.
Ready to get ahead of the next production delay?
By being well-prepared with a plan for procuring and managing materials, you can ensure that you have the supplies they need when you need them. Avoid production disruptions caused by material shortages and keep production costs down by mitigating the need to expedite shipments or make last-second arrangements.
Learn more about Manufacturing Supply Chain solution, the SPS Commerce solution for those involved in the manufacturing supply chain. Plus, read through the rest of the blog series for Manufacturing Supply Chain, with How manufacturers can eliminate the stress of frequent change, The importance of effective demand planning and A comprehensive overview of business manufacturing problems.
- A comprehensive overview of business manufacturing problems - November 19, 2024
- The importance of effective demand planning - November 19, 2024
- How manufacturers can eliminate the stress of frequent change - November 19, 2024
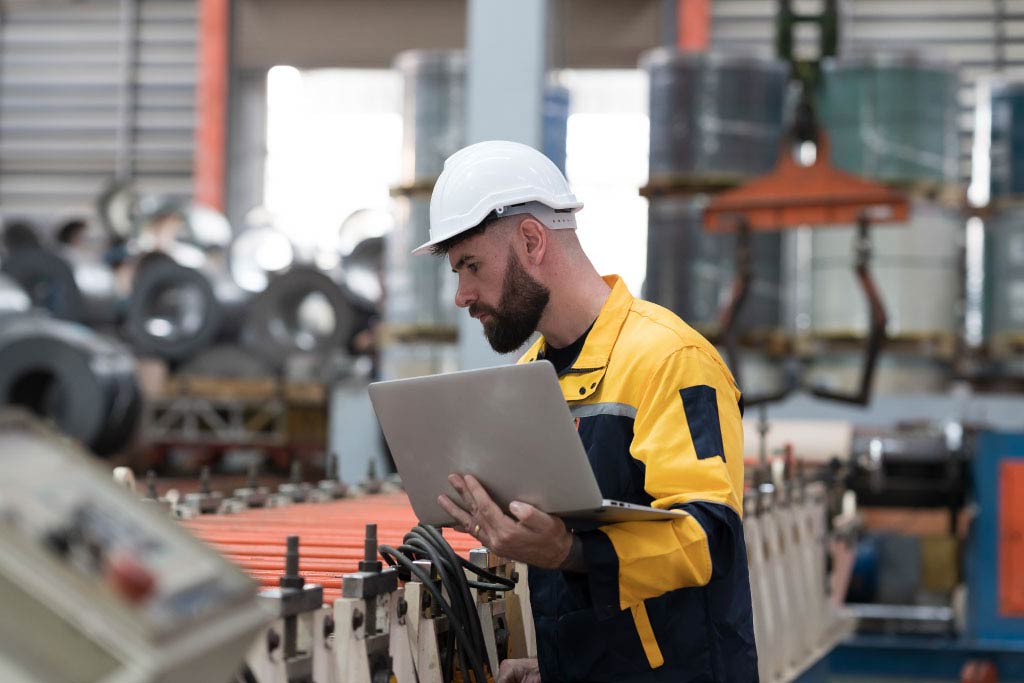
RELATEDÂ POSTS
How to tame volatile manufacturing su...
How to build an agile supply chain in...
How suppliers can align to retailersâ...