How to Modernize Your Warehouse Inventory Management Practices
Consumer demand for omnichannel shopping and faster product deliveries is intensifying the need for better warehouse inventory management. How can organizations use automation to get inventory in and out of warehouses (and to consumers) as quickly as possible?
Want to make inventory move more efficiently through your warehouses and distribution centers? Download our playbook or visit our website for more information.
The current state of warehouse inventory management
Manual inventory management requires multiple steps that significantly slow down the process of fulfilling orders. First, the carrier or supplier arranges for a delivery appointment indicating the size of the load and a list of the orders in the delivery. After a trailer pulls up with a shipment:
- The receiving team takes the packing slip and enters the information into their WMS or ERP system to locate the order details.
- Once they find the order associated with the shipment, they print the receiving documents (in some cases a customized barcode label with the bin location and item details).
- The receiving team counts cases, pallets and boxes to confirm what’s included in each shipment.
- Each shipment goes into a staging area.
- The putaway team either scans the pre-print barcode label or reviews the manual receiving documentation to determine the right bin location.
- The putaway team brings products to their appropriate bin.
- Finally, the received item count is entered into the WMS and PO receipt system. This may have been accomplished when the custom barcode was scanned but in other cases, the receiving report is manually entered into the system by data entry staff.
All of these steps are time-consuming and prone to errors. Unfortunately, these types of inefficiencies are extremely common in warehouses and distribution centers today.
Automation for greater warehouse throughput
Instead of the process above, what if you had data from your suppliers about what was in each shipment in advance. And what if each shipment included a shipping label with a scannable barcode, already provided, that specified the contents of each pallet or carton?
Getting advance visibility will allow you to staff each of your warehouses appropriately with the right amount of people to unload each trailer. It also notifies other resources in your organization that a shipment is in route and informs them of its content.
When a new shipment comes in, a worker could pull up on a forklift and scan the supplier-provided barcode label on the pallet or carton to begin to build content of the warehouse receipt. The scan would also display the appropriate bin location. One worker could handle the whole receiving and put-away process in an integrated, automated workflow.
Also, managing the receiving process in this manner would allow for any products in the receiving department to be rerouted to the shipping department if there are open customer orders needing to be shipped immediately.
This type of automation typically saves 15 minutes or more per pallet. That might not sound like much, but when you’re processing hundreds or thousands of pallets or cartons a day, the savings are significant. For many buying organizations, creating greater inventory management efficiency adds up to a multi-million dollar impact.
Two critical pieces of supplier information
Our work with hundreds of retailers, grocers and distributors shows that two types of data are critical for warehouse automation and throughput. These are the advance ship notice (ASN) and the GS1-128 (also known as UCC-128) label.
Automating warehouse inventory management is impossible without understanding what suppliers will ship, and when. The ASN provides data such as:
- What order(s) shipped?
- What items are being shipped and how many?
- When will the order(s) arrive?
- Does the shipment contain the complete order?
The supplier-provided GS1-128 labels work in tandem with the ASN, and contain information about the origin, destination and contents of the shipment. While neither ASNs or GS1-128 labels are new, many organizations have not yet fully embraced them. In a recent survey, less than one-third of respondents used barcoding of the majority of their items.
Working with your suppliers to implement ASNs and labels can be a great place to start improving warehouse inventory management. If you’re interested in learning how SPS can help you create a more efficient warehouse plan, visit our website or download our playbook.
- EDI compliance brings value for buying organizations - August 15, 2023
- What is Advanced Shipping Notice (ASN) in Shipping? - March 28, 2023
- Test new products online before stocking at retail stores - February 2, 2023
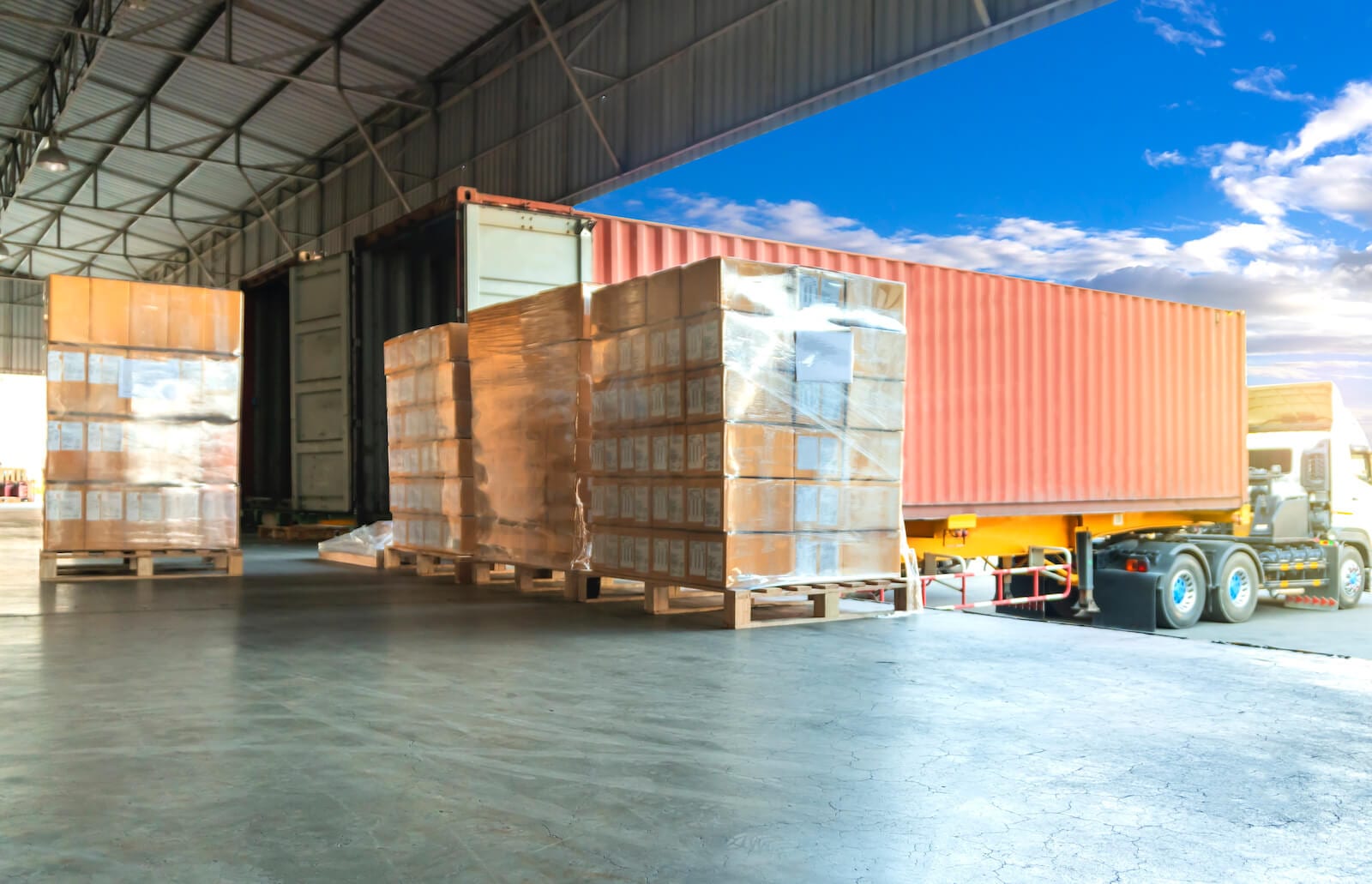
RELATED POSTS
Three takeaways from SuiteWorld 2024
Acumatica Summit 2024: A recap
How to get purchase order to invoice ...