Achieving operational harmony with automation
See how Crosley Brands transformed their EDI process with SPS Commerce, resulting in improved efficiency, greater reliability and a sharpened focus on strategic initiatives.
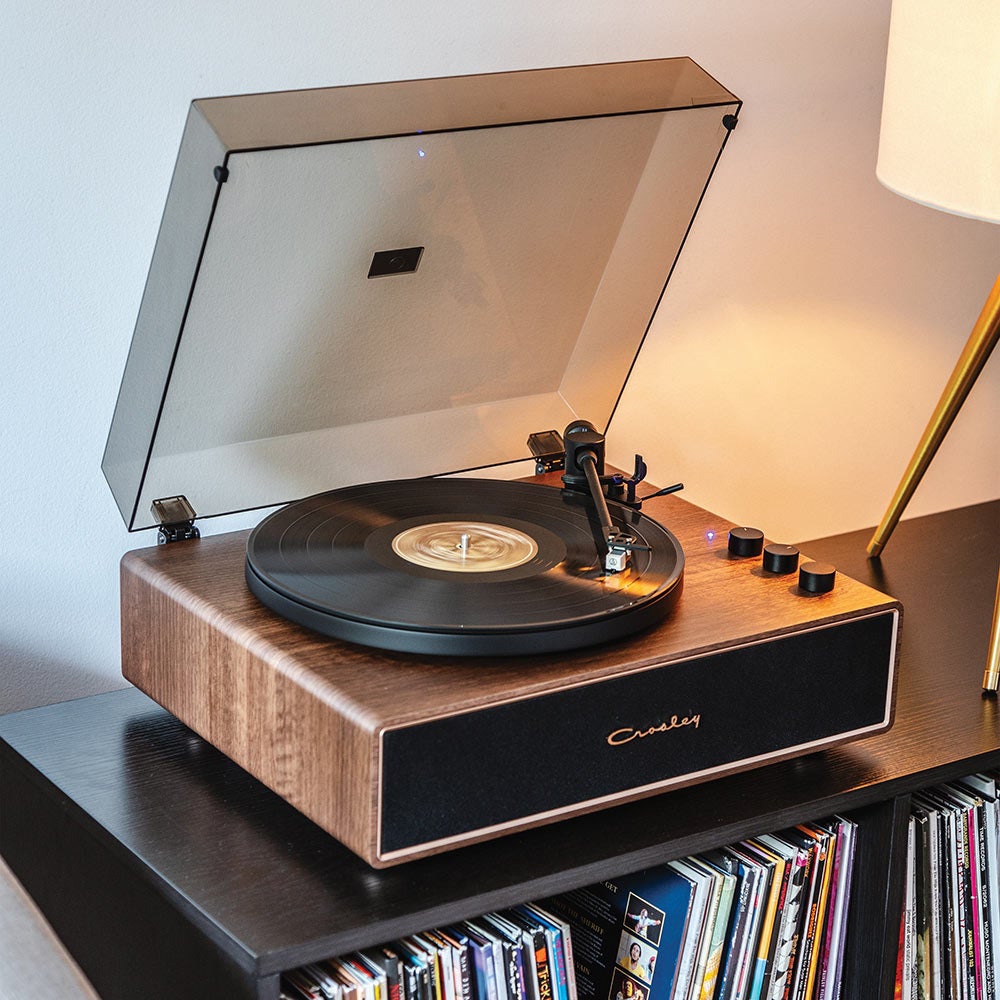
The challenge:
Eliminate time-consuming, manual EDI tasks to streamline operations and boost efficiency.
The solution:
SPS Commerce Fulfillment with System Automation for JD Edwards
The result:
With automation and a solid EDI process, Crosley Brands has freed up valuable time to focus on growth rather than routine maintenance.
The challenge
With automation and a solid EDI process, Crosley Brands has freed up valuable time to focus on growth rather than routine maintenance.
“Our goal for the last several years has been ‘manage by exception’. Where our teams don’t need to spend their time and resources doing repetitive mundane tasks. We’re looking for areas to improve and make the process seamless for them.”
– Guru Adivalli, VP of Information Technology.
The solution
Partnering with SPS Commerce provided Crosley Brands with a full-service EDI solution that helped them reach their “manage by exception” goals. Leveraging the right combination of people, processes and technology, SPS delivered a seamless solution tailored to meet Crosley’s unique business needs and the requirements of their trading partners. With a team of experts skilled in JDE and extensive ERP integration knowledge, SPS utilized pre-configured mapping structures that accelerated implementation and eliminated the need for complex customizations. By taking on project management responsibilities and minimizing Crosley’s involvement in mapping, SPS streamlined the process, reduced day-to-day disruptions and made the transition to true automation effortless.
“This was one of the few projects that we’ve handled where it went like it was promised from a project management and implementation perspective, which is a delight for me because that’s not the case a lot of the time. When you have responsive support and a process that works, that’s the best thing I could ask for.”
– Guru Adivalli, VP of Information Technology.
The results
Today, Crosley Brands spends significantly less time troubleshooting, freeing up their resources to focus on more business-critical tasks. The changes made to their EDI process have led to:
- Greater automation: The fully automated EDI process has eliminated bottlenecks and extensive maintenance, with teams only managing occasional exceptions.
- Increased efficiency: With manual work and maintenance off the to-do list, the Crosley team has significantly increased overall operational efficiency.
- Enhanced focus on growth: With support from SPS, the Crosley team can dedicate more time to planning for future success rather than fixing issues.
The transformation of their EDI process has freed up resources, time and energy, allowing Crosley Brands to prioritize growth and innovation over routine maintenance.
The biggest value of our partnership with SPS is that we’re truly managing by exception. You’re talking about maybe 10-15 minutes of work that entire week and the rest is just flowing.
– Guru Adivalli, VP of Information Technology.